Before
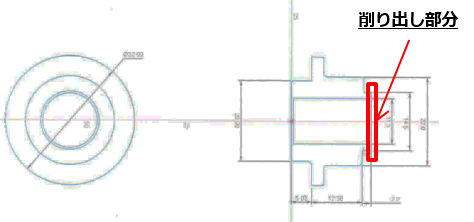
上記の製品は中ツバ形状部品で、一見、冷間鍛造による成形としては一般的な形状に見えますが、段付き形状となっており、かつ右端面における薄肉部分(厚み2.2mm)の成形が非常に難しいと言えます。その為、これまでは、鍛造による成形後、端面部分は削りだしによる加工が行われていました。
After
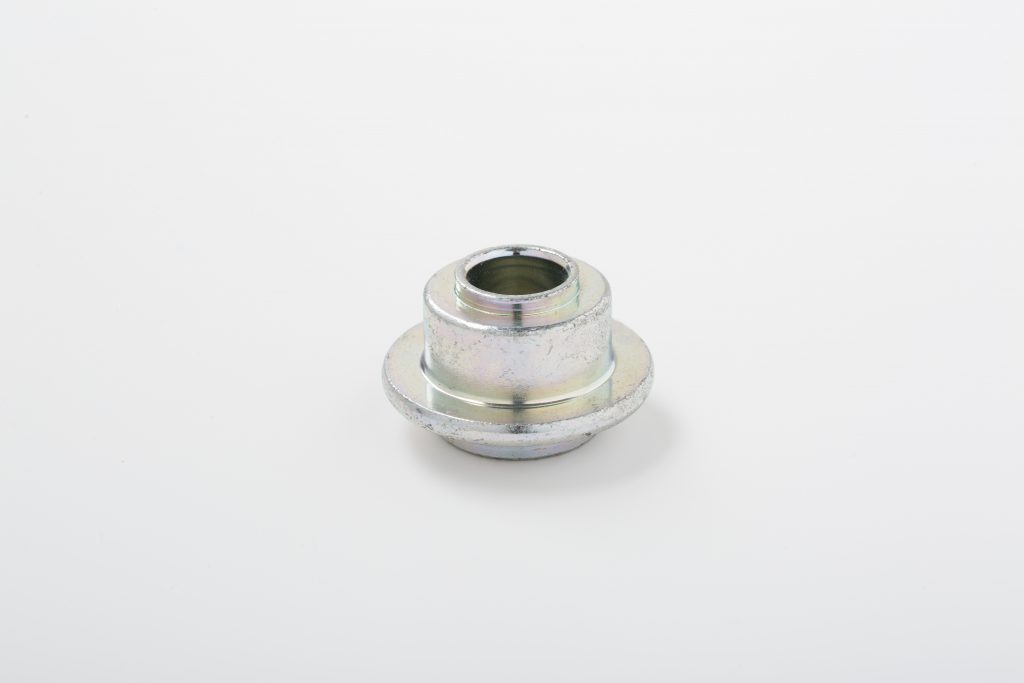
従来:冷間鍛造+旋盤工程
現在:冷間鍛造
コスト:2/3
こちらの製品に対しても、当社では切削レス化つまりオール鍛造化を実現しました。端面からの距離が短いことから一般的には切削込での提案となりますが、当社の場合には、金型の細かいメンテナンスや設計提案も行っていることから、薄肉異形状部品の冷間鍛造化を実現することが可能です。今回の事例の場合には、ロットが3万個であることから効果は非常に大きく、コストにして2/3程度のコストダウンに成功しています。
当社では、冷間鍛造では「難しい」もしくは「不可能」とされているような高精度部品の鍛造化に成功してきました。こちらの製品のように中ツバ形状でかつ、薄肉加工が部分的に必要となる製品も冷間鍛造+切削加工からオール鍛造化が可能となります。冷間鍛造における切削レス化はコストを大幅削減することになる為、量産品の場合にはコスト面で大きなメリットの提供が可能です。